Lowpass filters might not be grand or flashy, but they immensely impact many ground-breaking...
RF Engineer’s Guide to Microwave Filter
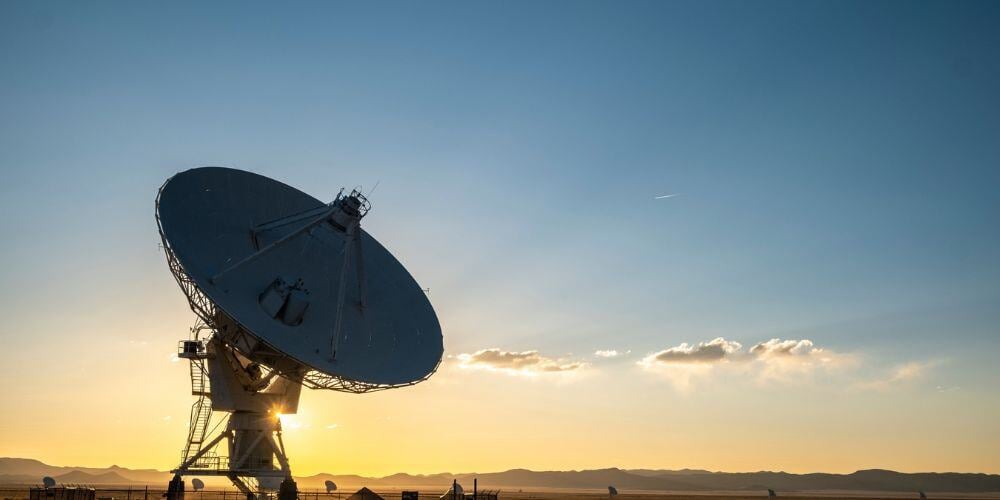
The RF engineering world is rapidly evolving and expanding. At the current growth rate, the RF filter market is predicted to be worth nearly $50 billion in 2031.
This surge in demand for microwave filters emphasizes the need for cutting-edge solutions that can meet challenges across industries such as military or commercial applications. For the progressive-minded RF engineer, this guide dives deep into questions surrounding microwave filters, their value, and how they’re evolving.
- Why Does My Defense Company Need RF Microwave Filters?
- How Have Evolving RF Tech Needs Transformed Microwave Subsystems?
- Which Emerging Applications Are Utilizing RF Subsystems and Components?
- How Can I Test My Bandpass Filter Design Using Diagrams?
- What Are the Factors to Consider When Choosing a Custom Microwave Bandpass Filter?
- What Are the Pros and Cons of Analog vs. Digital Bandpass Filters?
- Why is Hermetic Packaging Important for Microwave Filters and Components?
- What are the Pros and Cons of Different Microwave Filter Packaging Options?
- What are the Most Common Trade-Offs When Using RF Filters?
- What Challenges Does Miniaturization Pose in Integrated Microwave Assemblies?
- What Questions Should I Ask a Microwave Filter Company?
1. Why Does My Defense Company Need RF Microwave Filters?
RF microwave filters are indispensable in defense communications. They ensure clear and secure transmissions across applications such as radar, electronic warfare, and satellite communications. These filters excel in isolating specific frequencies and blocking unwanted signals. These help maintain the integrity of sensitive data and uninterrupted communication in environments densely populated with electromagnetic signals. This capability is very important in preventing data breaches in military operations.
Further, defense systems are often deployed in harsh and unpredictable environments. They undergo rigorous thermal and shock testing, designed to minimize signal degradation even under the harshest conditions. This robust design ensures minimal signal degradation even in the most adverse of conditions.
It’s also worth noting that RF microwave filters improve the functionality and precision of sophisticated electronic warfare and radar systems. They manage high power levels used in radar jamming and countermeasures, maintain signal clarity, and distinguish between friendly and adversarial signals. The enhanced rejection rates and improved signal-to-noise ratios of these RF microwave filters provide military operations with robust capability in their radar and identification systems.
2. How Have Evolving RF Tech Needs Transformed Microwave Subsystems?
The rapid evolution of RF technology – particularly with advancements like 5G and microelectronics – has significantly reshaped microwave subsystems. This evolution is driving the need for more refined filtering capabilities as systems push beyond traditional frequency bands towards the 100GHz mark and beyond.
-
Trend 1: Expanding Frequency Requirements: Solutions now need to handle the expanded spectrums, and microwave subsystems are adapting to these. The focus is supporting the robust requirements of 5G networks, including enhanced speed and data handling capacities.
Source: Q Microwave
-
Trend 2: A Demand for Microelectronics: The advancements of microelectronics reflects a broader trend towards miniaturization – which means a demand for more compact yet powerful devices. The challenge is in balancing the Size, Weight, Power, and Cost (SWaP-C) without compromising performance or cost-effectiveness.
-
Trend 3: High Performance Component Needs: The development of high-performance parts within microwave subsystems – such as RF upconverters and downconverters – shows the ongoing need of versatility. Microwave subsystems must operate across broader frequency ranges with increased efficiency and reduced power consumption.
The demand for microelectronics is growing significantly, reflecting their critical contribution to advancing defense and communication technologies.
As these systems develop, the importance of subsystems meeting the demands grows.
3. Which Emerging Applications Are Utilizing RF Subsystems and Components?
We are at a point where satellites can help predict natural disasters such as forest fires. RF systems and their components are central to this and other significant developments in disaster management, environmental monitoring, and national security. This is thanks to their ability to modulate, amplify, and refine signals.
In military applications, RF subsystems are used in developing counter-drone technologies to address the rising use of drones in surveillance and attacks. These systems are a non-destructive means to control or disable unauthorized drones.
“The need for counter-UAS weapons is so acute, according to the Pentagon’s top weapons buyer, that it now constitutes a ‘crisis.’”
- A Recent Breaking Defense Report
Similarly, modular RF designs are revolutionizing communication. These smaller and adaptable systems can be used in satellite communications and land-mobile radios. They are designed to be cost-effective, easily upgradable, and work to stay ahead of tech advancements without extensive overhauls.
Another new application of RF subsystems is found in space-based thermal imagery where they facilitate the acquisition and transmission of thermal data. The ability of RF subsystems to support satellite communication allows for efficient environmental monitoring, military reconnaissance, and even disaster management.
4. How Can I Test My Bandpass Filter Design?
Testing custom bandpass filter designs is important to ensure they perform reliably under various conditions. Here’s an overview of how to conduct a test:
-
Temperature Cycling: Filters must undergo temperature cycling to ensure they’re stable across extreme temperatures.
-
Vibration Testing: This test checks the ability of a bandpass filter to withstand and function amid intense vibrations. This is essential for filters used in high-speed vehicles like aircraft.
-
Burn-In Testing: This test identifies any potential failures in filter components that are expected to endure high power or long operational periods.
-
Leak Testing: For filters requiring hermetic seals, this test confirms the integrity of the seal against moisture and gas ingress.
-
Frequency Testing: Filters are tested with network or spectrum analyzers to ensure they meet the designed frequency specifications and perform correctly across their bandwidths.
Each type of testing is tailored to the specific requirements and anticipated use environments of the bandpass filters. The goal is to ensure each component meets the highest standards of quality and reliability before deployment.
5. What Are the Factors to Consider When Choosing a Custom Microwave Bandpass Filter?
The choice between a custom or standard microwave bandpass filter is an important decision for projects in aerospace, defense, and satellite communications. Custom filters are often required in high-risk environments to ensure ideal performance and signal integrity. These are the key factors to consider when deciding whether a custom solution is necessary for your RF system:
-
Tightness of Specifications: Custom filters are ideal for when exact specifications are required — such as sharp roll-offs or high rejection rates. It depends on the physical requirements of your product.
-
Volume vs. Cost: The decision between custom and off-the-shelf bandpass filters often depends on the balance between production volume and cost. Custom filters, while potentially more expensive, offer tailored solutions that can prevent future system overhauls. Meanwhile, standard filters might be more economical for large-scale deployments unless the requirements are specific.
-
Integration and Size: Custom filters can be designed to fit specific dimensions and integrate seamlessly with other components without sacrificing overall system design.
-
Lead Times: Custom filters, by nature, need longer lead times due to specialized design and testing.
-
Environment and Durability: Filters may need to withstand conditions, such as extreme temperature, high humidity, and corrosive atmospheres. Custom filters are designed based on various project requirements to ensure consistent performance despite exposure to unpredictable environments.
Should any of the aforementioned factors correspond to your project requirements, a custom microwave bandpass filter may be necessary instead of a standard model.
6. What Are the Pros and Cons of Analog vs. Digital Bandpass Filters?
Choosing between analog and digital bandpass filters involves weighing numerous factors such as signal-to-noise ratio, power consumption, and the need for reconfigurability.
Analog filters, used extensively in applications where real-time processing is vital — such as live audio and radar systems — offer zero latency and continuous signal processing. This means that the signal remains pure and unsegmented. This maintains its integrity and quality, which is particularly important in broadcasting and military technology.
Despite their benefits, analog filters are susceptible to noise and interference and are constrained by the physical properties of their components. That means they can degrade over time and affect performance. They also lack flexibility for applications with changing requirements. Once built, modifying their characteristics like cutoff frequencies requires hardware changes, which can be challenging.
On the other hand, digital filters are flexible and programmable. Their digital nature allows for easy adjustments in filter characteristics through software without physical alterations. This makes them adaptable to environments where filter specifications may change due to varying operational or environmental conditions.
Digital filters also offer precise and stable performance, unaffected by physical component aging or environmental factors, ensuring reliable long-term operation. However, they have drawbacks including latency from signal conversion, aliasing that needs careful pre-filtering, and generally higher power consumption and complexity from digital processing.
Choosing between analog and digital filters depends on the specific needs of the application and allowable trade-offs. For projects requiring immediate signal processing without delay, analog might be the preferred choice. On the other hand, digital filters might be more suitable for applications that benefit from high precision, stability, and the ability to adapt to changing requirements.
7. Why is Hermetic Packaging Important for Microwave Filters and Components?
Hermetic packaging provides a robust barrier that protects sensitive microwave filters and components from environmental hazards like moisture, contaminants, and extreme temperature fluctuations. This type of packaging is advantageous in fields such as maritime and space exploration. By sealing components in a controlled nitrogen atmosphere, hermetic packaging preserves their integrity while improving their performance.
The design of hermetic packaging involves selecting materials and sealing techniques to protect against environmental extremes. Consider the balance between the package’s size, weight, power, and cost. These factors are particularly important in applications where the reliability of technology must be maintained without adding excessive bulk or cost — such as satellite components or the military’s increased use of drones.
No matter how advanced RF technology gets, if it’s not protected, it’s worthless. As RF engineering continues to evolve, the role of hermetic packaging will become increasingly important in maintaining the functionality and longevity of RF systems.
8. What are the Pros and Cons of Different Microwave Filter Packaging Options?
The right microwave filter packing choice is foundational for the success of RF engineering projects. It impacts everything from signal integrity to system integration.
Packaging options vary, from standardized types that offer convenience and cost efficiency, to custom designs tailored to meet specific project needs. Here are the pros and cons of these different types of filter packaging:
Standardized Packaging
Pros:
-
Cost Efficiency: Standardized packaging reduces unit costs, making it a budget-friendly option.
-
Faster Delivery: Pre-defined designs and readily available materials speed up manufacturing, resulting in quicker delivery timelines.
-
Simplicity in Design: Straightforward packaging minimizes complexity in production and integration.
Cons:
-
Size Limitations: Fixed dimensions may not fit all project specifications, potentially limiting design flexibility.
-
Limited Customization: Standardized packaging may not meet specialized performance or environmental requirements.
Custom Packaging
Pros:
-
Tailored to Project Needs: Custom packaging allows precise modifications in shape, size, and material properties, ensuring a better fit for complex requirements.
-
Enhanced Durability: High-quality materials and reinforced designs improve the durability and longevity of the filter.
-
Improved System Integration: Custom designs ensure seamless integration into unique system architectures, optimizing performance.
Cons:
-
Longer Lead Times: The intricate nature of custom designs can extend production timelines, potentially causing delivery delays.
-
Higher Costs: Specialized design and materials increase the cost of custom packaging.
-
Increased Complexity: Custom packaging may introduce complexity in integration, requiring more time and resources.
-
Risk of Performance Issues: The wrong material or design choices can negatively impact filter performance, especially in high-stakes environments.
Source: Q Microwave
While the actual filter components are crucial, selecting the appropriate filter packaging is nearly as important. RF engineers weigh these advantages and challenges to meet vital project requirements.
9. What are the Most Common Trade-Offs When Using RF Filters?
The main challenge with RF filters is the trade-offs – primarily in the SWaP-C (Size, Weight, Power, and Cost) concept. When designing electronics and communication systems, engineers must consider the goals of performance requirements against the realities of physical and budget constraints. For instance, improving a filter’s power handling capabilities might require increasing its size, but that may conflict with the need for compactness.
Ultimately, the main priorities will be dictated by the specific industry or application. Smaller filters, such as those used in mobile devices or military devices, require high performance within limited physical dimensions. This often leads to higher costs due to the need for sophisticated materials and design techniques.
On the other hand, larger, less restricted designs allow for more robust performance but can be impractical in size-sensitive applications. Moreover, the choice of materials for custom RF filters impacts both the cost and performance of filters, with higher-quality materials ensuring better performance but at a higher price point.
10. What Challenges Does Miniaturization Pose in Integrated Microwave Assemblies?
There is a consistent drive toward the need for devices to perform increasingly complex functions within smaller forms across industries. This demand is particularly intense in sectors such as defense, space exploration, and broadband communications.
Miniaturization of integrated microwave assemblies tests the limits of the physical laws that govern electronic components. Achieving smaller sizes requires rethinking traditional design in order to simply maintain functionality and reliability.
As microwave assemblies shrink, the intricacies of design and manufacturing increase. Producing smaller, yet powerful, devices requires precise engineering and rigorous testing to ensure they meet the required performance standards. Thus, they are more expensive and often require long development cycles.
To find the right solution, RF engineers should consider focusing on specific use cases, such as hermetic packaging, rather than broad specifications. The goal is to design compact assemblies that perform reliably in challenging RF environments.
11. What Questions Should I Ask a Microwave Filter Company?
Designing and manufacturing RF filters and subsystems for military, space, or commercial applications is complex. The process involves complex decisions about materials, specifications, and testing protocols.
Given the sophisticated nature of RF engineering, it’s important to ask the right questions to determine a microwave filter company’s capability to deliver high-quality, reliable, and efficient solutions. Here are the important questions to consider:
-
How can you ensure reliability for my high-pressure application’s components?
-
How will my specific application requirements be met?
-
What are your typical lead times on prototype filters and subsystems?
-
How is packaging customized for RF filters or subsystems?
These questions will help you understand a company’s approach to design challenges, their adaptability to specific requirements, and their capacity to innovate and deliver on time. Use each question to inform whether the microwave filter company is a good match for your project’s unique demands and timelines.
Q Microwave: Your Partner in RF Filter Design
Q Microwave brings over 25 years of experience creating RF filters and subsystems. Our team possesses the expertise and important historical knowledge to address the complex challenges in RF technology. By partnering with us, you gain access to solutions finely tuned to your specifications. Our innovative technologies are designed to meet your specific needs. Learn more about our services and start optimizing your approach to RF systems today!