Somewhere above you in Earth’s orbit is a satellite transmitting weather maps on 401-402 MHz.
3 Ways to Test the Quality & Bandwidth of a Bandpass Filter
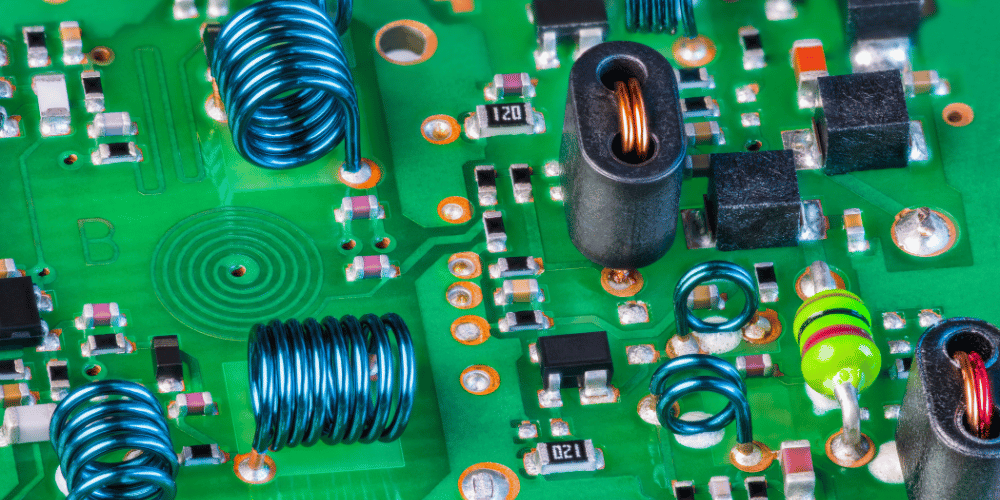
While an RF bandpass filter may be small in size, its importance cannot be underestimated in the world of modern technology. Engineers know that they need a specific bandwidth in their bandpass filters that can accurately block and receive a precise range of frequencies.
But when an off-the-shelf filter doesn’t match what you need, that’s when manufacturers come into the picture. At Q Microwave, we understand that the quality of your RF filter is everything to your application. When you need a custom filter, we are entrusted with not just crafting these essential filters, but also rigorously testing them to meet your high standards.
But what types of testing do we do to ensure the bandwidth of a bandpass filter is the right length to capture and reject frequencies? In this article, we will cover the three main types of tests our team performs.
Let’s start with one that is often crucial for military applications: High-stress environmental testing.
Test #1: Environmental Testing
Whether stationed in the scorching heat of a desert or the unforgiving cold of mountainous terrain, the reliability of a filter under stress is non-negotiable.
While technology has become more advanced – some weather radar applications can determine the shape of a 6-millimeter raindrop from more than 8 miles away – the need for environmental resilience has only grown. The ability to work under high-stress environments is a cornerstone in the development of RF technology, particularly with electronic warfare applications.
However, it’s not just harsh climates that are affecting RF technology and its applications. Climate change poses broader challenges to the operation and longevity of radars and their components. Consider the material and design of RF filters, for instance. These components, originally designed for certain temperature ranges, might now face conditions far beyond their initial specifications due to rising global temperatures. This scenario raises concerns about their longevity and effectiveness in increasingly extreme environments. For historical reference, three of the long-range radar stations operating in Alaska grappled with climate-driven threats to their RF technology infrastructure.
“In 2007, the New York Times reported that three short-range radar sites in Alaska were closing because, in part, soil erosion was causing the ground to crumble beneath them. A 2014 report by the Government Accountability Office found that the installations are seeing erosion that defense officials didn't expect until the year 2040.”
- Zachariah Hughes, “How Climate Change Is Affecting Alaska's Military Radar Stations” via NPR
While a filter can’t be tested against the ground falling away beneath it, these examples highlight the broader issues that climate change presents. As temperatures rise, a filter placed in an already hot environment might degrade faster than anticipated, potentially compromising the integrity of communication systems that were built decades ago. This necessitates a reevaluation of how we test RF filters, not just against current environmental extremes, but also against the evolving and unpredictable nature of climate change.
But it’s not just the bandpass filters within radars and broadband applications that are subject to harsh climates. Even space satellites face their own unique set of environmental challenges. The vacuum of space is one of the harshest terrains. That’s why satellite technology requires a level of durability that can only be assured through environmental testing.
Test #2: Frequency Testing
Besides testing for the outside environments, a bandpass filter’s cutoff frequency must be tested to ensure it performs according to its required specifications. This type of testing is vital, as the world of electromagnetic frequency has never been busier!
To validate the bandwidth of a bandpass filter, the integrity of the filter material is scrutinized through a series of tests throughout our entire design process. No matter what the bandpass filter type is, we subject various materials, including ceramic resonators, combline filters, and lumped-element filters, to stringent testing. Each filter type has unique properties and testing applications and must be tested with these in mind.
In scenarios where communication and detection systems must function without issues, the quality of the filter’s materials cannot be left to chance. Each type of material is therefore tested and retested.
Not sure if you need an off-the-shelf or custom microwave filter? Check out this article to see if a custom RF filter is a necessity for your project!
Test #3: Multiple Rounds of “Final” Tests
While this is not a ‘type’ of filter test, it’s important enough in our process to discuss it. Multiple rounds of testing are an important aspect of filter manufacturing. For example, if a military radar doesn’t work due to technical problems, it could cause significant delays and cost millions of dollars.
Once a filter’s materials are ordered and arrive at the manufacturing site, an engineering team will perform a final tuning or alignment of the filter. Then, it will go through additional environmental requirements as mentioned above.
You might think that after the first few rounds of testing, the filter is ready to go. But our team at Q Microwave is so passionate about ensuring that a filter is high quality that it has multiple rounds of “final” tests.
And so, after that second round of testing, the filter will once again go through any needed mechanical and environmental testing procedures. Then it will be marked and labeled, then another round of testing will be done.
Of course, once the filter is assembled, it must pass another final inspection! This in-depth process has secured our RF manufacturing company as one of the leaders in the industry for over twenty-five years.
Conclusion: Choose a Trusted Manufacturer for Your Filter Needs
Through a methodical testing process, RF filter companies must dedicate themselves to delivering RF filters that not only promise performance but also persist through the harshest of conditions.
At Q Microwave, our tests are designed with a singular goal in mind: to deliver RF filters that meet and exceed the challenges they will face in the field. That’s why, by the time a custom RF bandpass filter reaches our customers, it has traversed a multitude of tests.
As you seek a partner for your RF filter needs, consider the depth of dedication to quality assurance that our testing exemplifies. Trust in a manufacturer whose commitment to excellence is proven through the most rigorous of trials, ensuring that when an RF bandpass filter reaches you, it's not just one component – it's a cornerstone of your project's success.
Reach out to us to learn more about our design process and how our team of kickass engineers can help with your next project!