Designing and building RF filters and subsystems can be a complex process. The components selected...
The Pros and Cons of Different Types of Filter Packaging
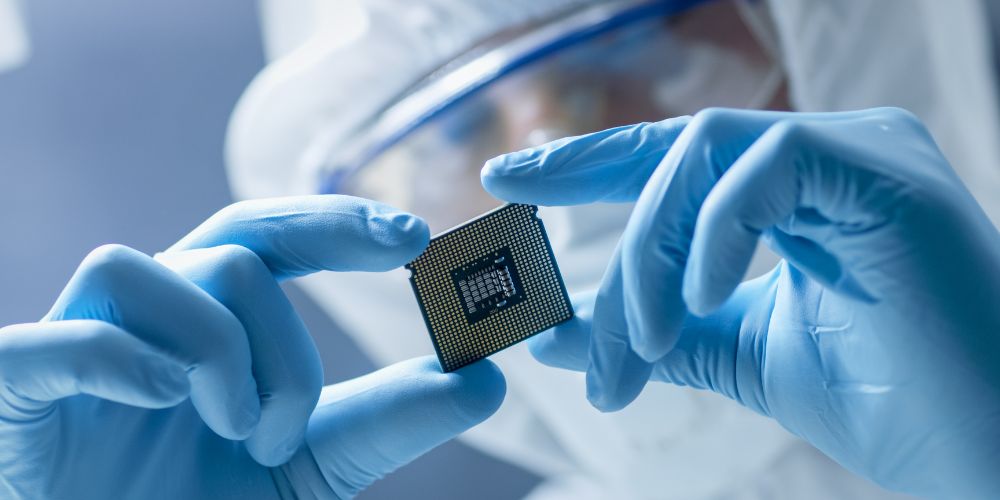
Picture this scenario: You’re an RF engineer tasked with a crucial project – designing an application that’s both efficient and cost-effective. The stakes are high, and every component matters especially in the RF subsystem. The modern world of frequencies is noisy and cluttered, and the filter we create must cut through.
The catch is that, while the actual filter components matter, choosing the right filter packaging is almost as critical. When you partner with our engineers, it’s not just about fitting your requirements into a budget-friendly design, but also optimizing for performance, managing the needed materials, and meeting project deadlines. This includes an often forgotten variable: the filter’s packaging.
Understanding the pros and cons of different types of filter packaging is vital for making the right decision for your project. In an industry that’s projected to grow nearly 17% by the end of the decade, knowing what packaging type will best suit your needs can give your custom applications an edge.
Understanding Filter Packaging
What exactly is filter packaging? If you’ve ever ordered a subsystem component before, you might not have paid attention to the actual material it came in .The packaging shields the filter, affects signal integrity, and determines how well the filter integrates into your system.
Making sure your standard or custom RF filters are protected increases both shipping efficiency and the quality of your components.
There are two categories of filter packaging: standardized and custom packaging. The former offers familiarity and ease of integration, while the latter offers tailored solutions for specific RF filter requirements, like size. Each packaging type serves a specific purpose depending on your timeline and specific project needs.
There are numerous options of cost-efficient custom packaging shapes and material options, such as the following:
-
Planar/MicroStrip
-
Formed Lead Configuration
-
Wire Bondable
-
PWB SMT
-
SMA
-
GPPO
-
And more!
However, it’s worth noting that not every custom or standard packaging option is available from every microwave filter manufacturer.
Source: Q Microwave
Pros of Utilizing Different Types of Filter Packaging
Selecting the right type of filter packaging is a must in RF engineering. Each type offers unique advantages, contributing to the overall functionality and success of the project.
Variety of Materials
The wide array of available materials means meeting the specific needs of your project. That could be a demand for high thermal conductivity or specific dielectric properties. The right material choice in filter packaging will significantly improve the filter’s performance and longevity.
Standardized Packaging
Standardized packages are a budget-friendly choice. They’re produced in larger volumes, bringing down the unit cost. For projects where price is a key concern, this is a gamechanger. Further, standardized options streamline the manufacturing process, leading to faster delivery. This efficiency means you can have prototype units in hand within 4 to 8 weeks of contract acceptance. When deadlines loom, you can operate confidently with your clients.
Customization Flexibility
However, for more specific solutions, custom filter packaging means flexibility and tailor-made solutions that precisely fit the unique requirements of your project. This means every aspect of filter packaging – from shape and size to material properties – is optimized how you want it. This is advantageous for complex or unconventional projects.
Enhanced Durability and Protection
High-quality materials and well-designed packaging can greatly improve the longevity and reliability of the filter, especially in harsh or demanding environments. This means better resistance to physical objects, environmental stressors like moisture and temperature fluctuations, and electromagnetic interference. This saves on maintenance and replacement costs, and improves reliability.
Filter Packaging Variables from Q Microwave
Cons of Utilizing Different Types of Filter Packaging
While the benefits of various filter packaging types are clear, you must know their limitations. Understanding the drawbacks will help make informed decisions in the design and implementation of RF systems.
Size Limitations
Standardized packaging, while cost-effective, comes with predefined dimensions and shapes. This can pose constraints for RF filters that require unique or custom sizes to fit specific applications. Engineers may be limited by these size restrictions, which may mean a more customized – and potentially more expensive – packaging solution.
Custom Packaging Delivery Time
Customization comes with more steps. This means the nature of custom packaging could mean longer production times. The delivery timeline can vary significantly based on the component’s size, shape, and material. Our team at Q Microwave will always be upfront with you about timeline expectations, and we have a history of shortening timelines when we can for urgent needs.
Availability of Packaging Options
Not all RF filter manufacturers offer a wide range of packaging options. This limitation can be a hurdle, especially if your project requires a specific type of package that your go-to manufacturer doesn’t provide. We recommend that engineers source from multiple vendors or trade off on their requirements, which might lead to additional costs.
Complexity in Application Integration
Custom packing solutions – while tailored to your application’s specific needs – can mean tricky system integration. They might require additional design modifications or adjustments in the surrounding subsystem. That could add time during the assembly phase.
Risk in Performance
Different packaging materials can impact the performance of the filter. For instance, some materials might excel in thermal performance but lack in electrical properties. Similarly, the physical design of the packaging could affect the filter’s ability to handle certain frequencies or power levels. Navigating these trade-offs requires a deep understanding of both the application requirements and the inherent properties of the packaging options.
Your Filter Packaging Choice Made Easy
The right RF filter packaging can change the direction of your application – but the variety of materials and approaches can be time-consuming to sort through.
That’s why we’re here to help. With over 25 years of experience, the Q Microwave team is here to help you choose the most suitable RF filter packaging material.
Don’t let the trade-offs of filter packaging slow down your project. We’ll bring your vision to life. Don’t wait to take the first step toward the successful implementation of your RF filter requirements.
Learn more about how we create RF filters!