Lowpass filters might not be grand or flashy, but they immensely impact many ground-breaking...
How Q Microwave Manufactures Lowpass Filters
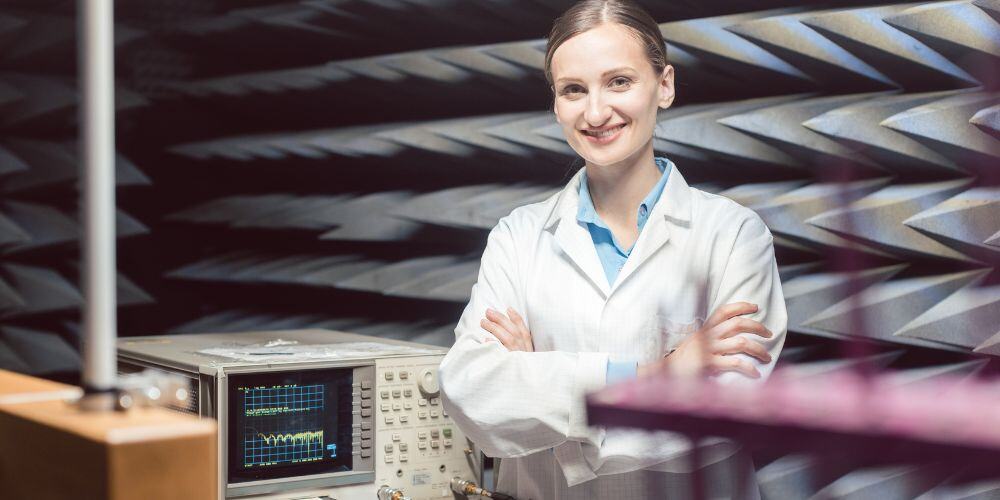
For specialized projects requiring precise lowpass filter characteristics, custom solutions offer significant advantages over off-the-shelf components. These custom lowpass filters are critical in RF applications, such as communication systems and signal processing, where filtering unwanted high-frequency noise is essential.
Thankfully, custom RF manufacturers like Q Microwave can produce and deliver filters tailored to your project requirements. Their high-quality manufacturing processes ensure that the filters meet the exacting standards required for optimal operation in demanding RF environments.
With the RF filter market rapidly expanding at a CAGR of 16.70%, there’s no shortage of suppliers. This growth indicates that more companies are entering the market to meet the rising demand, increasing the variety of available suppliers. The biggest roadblock, however, is finding a reputable partner whom you can trust with design specifications. Can they meet the precise cutoff frequencies and sharp roll-offs necessary to filter unwanted high-frequency noise in specialized communication systems?
To help RF engineers reach an informed decision, we’ll provide an insider’s look at Q Microwave’s meticulous manufacturing process. With 25+ years of experience in RF engineering, Q Microwave ensures that each step meets rigorous quality control measures and standards, assuring optimal performance, reliability, and longevity.
We’ll outline the structured process at Q Microwave, from initial design to final delivery. Our goal is to help engineers manage project timelines effectively without compromising quality control.
Step 1: Developing the Initial Design
The initial phase involves detailed design development. Our team collaborates closely with RF engineers to discuss the project’s design specifications. Serving a diverse range of clients across industries such as military defense, broadband, and space satellite technology, we understand that specialized projects come with unique requirements.
Once we fully understand your team’s unique needs, we’ll determine the most appropriate filter material—such as ceramic, coaxial resonators, or surface-mount devices (SMDs)—for your components.
Our team generally assesses the following factors:
-
Insertion Loss: We meticulously design and test our filters to minimize signal loss within the passband. By using advanced simulation tools and precision manufacturing techniques, we ensure that our lowpass filters maintain signal integrity and efficiency.
-
Cutoff Frequency: Our engineers set precise cutoff frequencies by carefully selecting and tuning filter components. We use state-of-the-art equipment to measure and verify that the filters effectively attenuate unwanted high-frequency signals to provide clean and accurate signal processing.
-
Power Handling: We evaluate the filter’s ability to handle the required power levels without degradation or failure, which is vital for reliable performance in demanding applications.
-
Environmental Stress Testing: This includes thermal and stress testing to ensure filters can operate reliably without degradation or failure in demanding applications.
General lead time: 3 to 5 working days
After designing the initial schematic of your lowpass filter, we’ll create an accurate simulation of the final product and provide you with an S2P file that describes the frequency response of the filter. This allows you to verify our evaluations and ensure that the proposed design meets both your short- and long-term project needs.
We will only proceed once you are fully satisfied with the results. Our team will closely collaborate with your RF engineers to ensure that the finalized schematic design aligns with your projected specifications.
From here, we can prepare an initial quote, set a feasible timeline, and calculate the additional testing requirements needed.
Step 2: Confirming the Preliminary Quote
For engineers, RF filter cost is a critical factor in determining the feasibility of any project. However, when manufacturers delay providing quotes, clients are put in a difficult position after investing significant resources in planning.
At Q Microwave, we present a comprehensive preliminary quote upfront. If you are satisfied with the initial design schematic of your lowpass filter and wish to proceed, we will break down the pricing and specifications for the entire project. This ensures transparency and allows you to make informed decisions without unnecessary delays.
Before finalizing any project, we offer clients detailed initial design concepts, comprehensive mechanical outlines, and well-considered recommendations. This meticulous approach also ensures full transparency and helps prevent any unexpected cost increases, giving you a clear understanding of what to expect.
Our goal is to ensure you are fully informed and confident in the project's scope and details before moving forward.
Step 3: Manufacturing Process
After the preliminary quote is approved, we can begin manufacturing your custom lowpass filter. We’ll assign a dedicated point person who will work closely with you throughout the project to address any concerns that may arise.
Our specialized engineers at Q Microwave will thoroughly review your finalized design requirements for the electrical and mechanical components needed. We’ll outline the entire manufacturing process in detail and break down the costs involved. The general lead time depends on the availability of materials on-site. We always strive to meet or exceed typical industry delivery times.
If vendor procurement is required, we’ll manage your expectations accordingly. Likewise, our team will prepare the initial documentation for assembly and testing to ensure that time isn’t wasted while waiting for materials.
Once the materials arrive, our team compiles them into an assembly kit. The Q Microwave assembly team will then follow the lowpass filter schematic documentation for construction, testing, and cleaning.
Fine-Tuning Lowpass Filters for Specialized Design Schematics and Compliance
The initial output will undergo rigorous fine-tuning to ensure it meets your specific requirements for frequency response, attenuation, environmental conditions, and insertion loss. We perform additional tests, including thermal, shock, and altitude testing, as needed. The team only proceeds once the precise specifications detailed in your schematics are achieved.
After thorough evaluation, we mark and label the filters for the final round of compliance testing. Q Microwave ensures that all lowpass filters comply with relevant industry standards and certifications, such as AS9100, for quality management systems, IPC A-610, and J-STD-001.
Step 4: Handling Post-Delivery
To ensure client satisfaction, Q Microwave bills the client only after the final lowpass filter is shipped.
The final bill may include non-recurring engineering (NRE) charges, which cover the costs of documentation and design phases for new products, including research, conceptualization, and development.
NRE costs are incurred only during the initial phase of a project. For repeat orders or mass production of the same lowpass filters, we reference the preceding schematics to eliminate the need for additional NRE charges.
That said, you can be assured that you won’t see any significant changes from the initial quote. Your point person will diligently update you about costs from the outset of the partnership.
Post-Delivery Check-Ins and Satisfaction Ratings
At Q Microwave, client feedback is invaluable. We encourage clients to provide feedback and ratings based on delivery time and product quality. This input helps us continuously refine and improve our processes and lead times.
Our company takes feedback seriously. We strive to exceed our client’s expectations, fostering long-term partnerships and delivering superior lowpass filters consistently. Your satisfaction drives our commitment to excellence in every project we undertake.
Q Microwave: Precision and Quality in Lowpass Filters
Quality is paramount when securing lowpass filters for specialized projects, yet suppliers rarely disclose their manufacturing processes. This lack of transparency leaves RF engineers uncertain about the quality controls in place. At Q Microwave, we aim to provide clarity by offering an inside look into our fast yet meticulous and rigorous manufacturing process.
Our team delivers the highest-quality lowpass filters tailored to your exact design specifications with competitive lead times. Through continuous innovation and stringent quality control, filters are tested to maintain long-term performance in various environmental conditions.
Share your project details with us and learn about our RF filter offerings today.