Designing and building RF filters and subsystems can be a complex process. The components selected...
The Cost Factors of Microwave Filters & Integrated Products
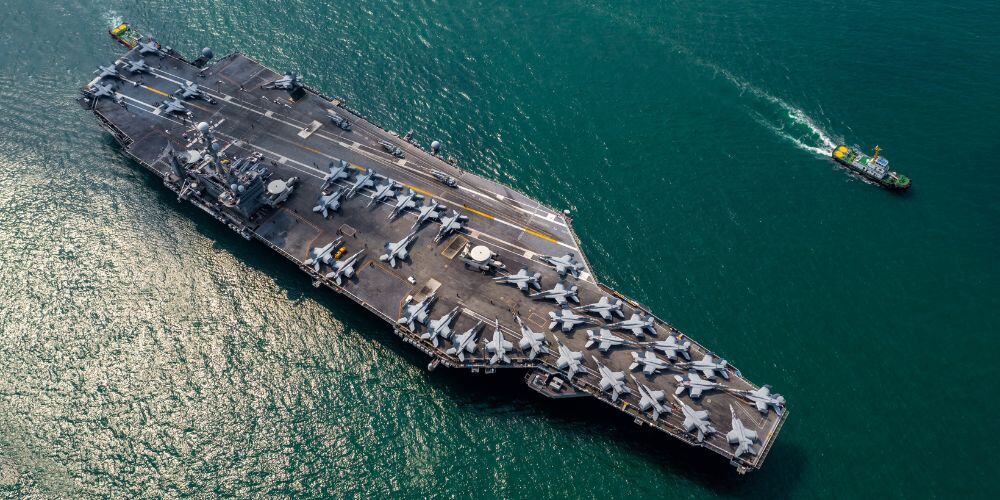
RF engineers working in critical sectors understand the need for high-performance microwave filters. Poorly specified hardware can cause system-level concerns—risks these sectors can’t afford. To ensure long-term subsystem reliability, RF components must meet essential performance criteria like frequency response, power handling capabilities, and rejection ratios.
RF subsystems in military applications exemplify the critical importance of hardware integrity. Given their essential functions in satellite communication, missile guidance, and radar detection, it is imperative that each component adheres strictly to specified performance standards. Neglecting even minor considerations, such as environmental tolerances, can lead to significant operational failures.
Unfortunately, stringent requirements often clash with tight budgets and time constraints. Understanding the key cost drivers detailed in this discussion can enable more accurate budget forecasts, facilitating a smoother and quicker RF filter procurement process.
In this article, we’ll discuss the key considerations that affect the cost of microwave filters and integrated products.
Key Cost Factors for Microwave Filters and Integrated Products
As RF engineers seek to optimize the performance of microwave filters within their projects, understanding the underlying cost factors becomes essential. These costs are influenced by a range of potential trade-offs, from material selection to manufacturing techniques. This section delves into the primary cost drivers in the production of microwave filters, offering insights into how each aspect contributes to the overall expense.
1. Material Cost
Here’s how material selection directly affects the cost of microwave filters:
-
Filter Topology: Different filter designs require varying amounts of materials. For instance, combline filters, known for their structured metal layers of aluminum or brass, typically incur higher costs due to substantial metal usage.
-
Material Purity: High-performance filters, especially those for demanding space and military applications, often require advanced ceramics with enhanced purity to better withstand harsh environmental conditions such as extreme temperatures, corrosive substances, and moisture exposure.
-
Material Availability: Market availability could drive up material costs. Rare, hard-to-manufacture compounds like Gallium Arsenide (GaAs), favored in high-frequency applications for their high electron mobility, are prone to price fluctuations, and supply chain constraints can make procurement take longer.
-
Substrates and Coating: The base material, typically a specialized PCB, and any protective coatings such as epoxy or parylene contribute to the cost of the filter.
2. Manufacturing Process and Technology Used
For custom microwave filters, the processes required for manufacturing and fabrication increase the overall cost per unit. Here’s what RF engineers should consider:
-
Precision and Tolerance: Microwave filters designed for high-frequency applications demand precise tolerance specifications during fabrication. To meet these requirements, manufacturers must invest in specialized equipment such as high-precision milling machines and advanced photolithography systems. Additionally, the operation of these tools demands highly specialized technical expertise.
-
Process Complexity and Yields: Fabricating custom filter topologies may involve intricate processes, such as micro-machining, thin-film deposition, and hermetic sealing. Even minor deviations can affect filter performance with these systems. This level of complexity can increase the average cost of each functional unit.
-
Specialized Facilities: Microwave filters for critical applications, e.g., aerospace, telecommunications, and military, are typically manufactured in cleanroom environments and facilities. RF manufacturers need a controlled atmosphere to ensure material stability. While these stringent conditions enhance filter reliability and durability, they also raise manufacturing costs.
3. Research and Development (R&D)
Designing and developing custom microwave filters comes with significantly higher R&D costs for these reasons:
-
Simulation: Complex project specifications for frequency response, rejection levels, and power handling, among other factors, require advanced simulation expertise. Standard simulations might not account for real-world factors. Apart from creating the overall filter model, engineers must also meticulously design their individual components and compute for optimal circuit interaction.
-
Prototyping and Iteration: Complex filter designs necessitate comprehensive simulations followed by extensive prototyping phases. Each iteration involves testing and refining to ensure the filter performs reliably in its intended application, adding to the cost.
-
Leveraging Pre-Existing Designs: For fast, cost-efficient RF solutions, engineers can explore off-the-shelf microwave filters and existing component designs. This approach can substantially reduce R&D time and costs by eliminating the need to develop bespoke solutions from scratch.
RF engineers shouldn’t have to worry about designing their filters alone. By partnering with an experienced RF filter and subsystem manufacturer, engineers can ensure that filter designs meet precise specifications and performance requirements effectively.
4. Design Complexity
The total cost of your custom filter primarily depends on its design complexity. More sophisticated designs with intricate specifications substantially increase expenditures in raw materials, manufacturing, and R&D.
-
Transfer Function and Topology: Apart from topology, RF engineers should note that achieving their optimal transfer functions (e.g., Chebychev for sharp cutoffs) entails specialized fabrication processes. Filters operating at higher frequencies are particularly susceptible to parasitic effects and interaction issues, which can compromise performance and escalate costs.
-
Size Constraints vs. Performance: Lower frequencies are hard to achieve with smaller topologies. If you need precise, complex filter specifications for tight space constraints, expect higher costs for extensive R&D and sophisticated fabrication techniques.
-
Lower Yields: The complexity of the manufacturing process for intricate filter designs typically results in lower yields. This not only extends production time and increases costs but also requires compensating for these lower yields through additional resources.
Get a Quote on Microwave Filters and Integrated Products
For most RF engineers, cost is one of the most critical factors to consider when procuring components, yet it’s also discussed last. What’s worse is that some manufacturers are not transparent about how costs are derived. By demystifying the key cost factors involved in microwave filter production, this discussion aims to equip RF engineers with the knowledge necessary to navigate these complexities.
At Q Microwave, we’re here to help, which is why we believe it’s crucial to offer transparency into how our microwave filters are priced.
Whether you urgently need off-the-shelf microwave filters or customized components suited to your specific needs, our RF design and construction specialists have you covered. Explore our microwave filter offerings!