Lowpass filters might not be grand or flashy, but they immensely impact many ground-breaking...
5 Lowpass Filter Design Best Practices for Optimal Signal Quality
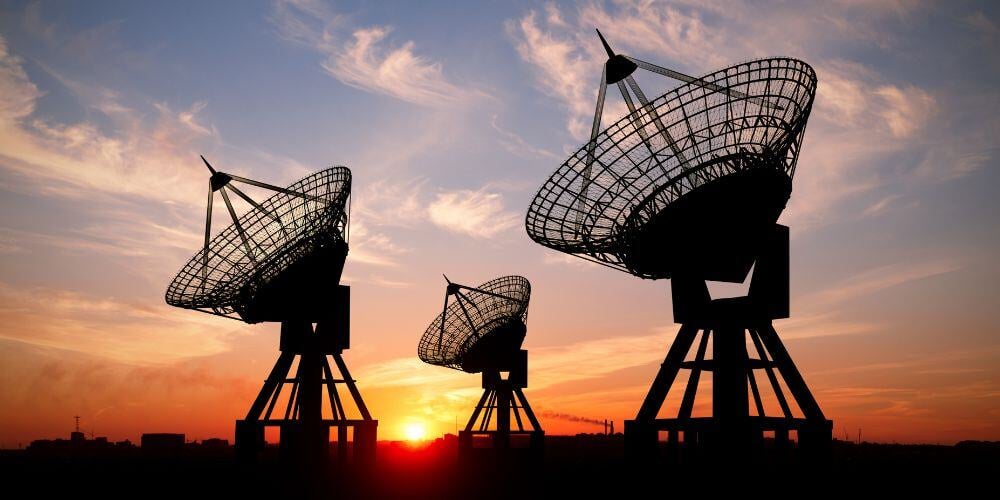
The modern world is so interconnected that a robust and reliable signal has become an expectation. Technology drives nearly every aspect of our daily routines, and most activities depend on stable communication.
With the RF spectrum becoming crowded due to the proliferation of connected devices and wireless applications, RF engineers must find ways to optimize spectrum usage efficiently. This means developing new methods to design filters, mitigate interference, and eliminate unwanted noise across different frequency bands.
Lowpass filters are crucial to attenuating unwanted harmonics and minimizing spurious signals that can degrade overall system performance, particularly in high-frequency applications. However, certain situations require more than standard off-the-shelf filters to meet specific performance demands.
Engineers must follow best practices in filter design to overcome RF interference issues and meet stringent performance requirements. Here are five best practices Q Microwave follows to enhance lowpass filter designs and maintain optimal signal quality.
Best Practice 1: Select Accurate Lowpass Filter Design Components
Selecting the right components is essential for a lowpass filter design to preserve signal quality and minimize noise. Inductors and capacitors, for example, set the filter’s cutoff frequency to block unwanted high-frequency signals. Inductors restrict high frequencies while allowing low frequencies to pass through. Meanwhile, capacitors divert high frequencies to the ground, preventing them from reaching the output.
Capacitors with stable values prevent signal degradation by keeping the frequency response consistent, even under variable conditions. Using stable components lowers the risk of frequency drift and provides predictable filter behavior, which is particularly important for high-frequency applications.
Component Selection Tips for Optimum Lowpass Filter Performance
A lowpass filter's performance heavily depends on its components' quality and characteristics. High-quality components help minimize parasitic effects,, which is critical to maintaining optimal signal performance and reducing unwanted interference. Parasitic inductance and capacitance in military radar systems can cause signal degradation, reduce detection accuracy, and make systems susceptible to interference from enemy electronic countermeasures.
Here are some practical steps to optimize your lowpass filter's performance:
- Choose capacitors with low equivalent series resistance (ESR) and temperature stability to maintain a consistent and stable cut-off frequency. High ESR capacitors can increase the ripple, an important parameter affecting capacitors' performance and behavior, particularly in high-frequency applications.
- Opt for resistors with low tolerance levels (or tighter tolerances) to reduce signal variations and achieve predictable filter performance.
- Use inductors with low core losses and minimal parasitic capacitance, such as equivalent parallel capacitance (EPC), to maintain the filter’s intended frequency response even at higher frequencies.
Best Practice 2: Set an Appropriate Cut-off Frequency
Accurate cut-off frequency selection is fundamental in filter design. If you set it too high, unwanted high-frequency noise may slip through. If you set it too low, you might lose essential signal parts.
Generic Lowpass Filter Response Cut-Off Frequency via Electronics Notes
RF engineers working on high-frequency ranges or critical projects, such as military or space applications, must precisely determine the appropriate cut-off frequency to maintain signal integrity. A communication satellite, for instance, must maintain stable connections despite harsh space environments. Military applications, on the other hand, must resist electronic countermeasures.
Determine the correct cut-off frequency for these demanding applications by:
- Identifying the frequency range that requires preservation and the frequencies that should be attenuated.
- Utilizing simulation software to model and verify the cut-off frequency under different conditions.
- Testing in the filter's intended environment to verify that the chosen cut-off frequency effectively meets application requirements.
Best Practice 3: Match Impedance Properly
When the impedance of a filter does not match that of the connected circuit, a portion of the signal is reflected to the source instead of continuing through the filter. Reflection can cause interference, echoes, or noise that degrades the quality of the original signal.
Impedance mismatch also causes inefficient power transfer between stages of a circuit. Residual energy is either reflected or lost as heat, reducing the overall power of the transmitted signal.
Measuring impedances and adjusting components to match values can mitigate impedance mismatch and help maintain clean signal transmission.
Best Practice 4: Minimize the Parasitic Elements
Parasitic inductance and capacitance degrade filter performance at higher frequencies, causing unwanted resonances, signal attenuation, and shifts in the cut-off frequency. Lay the circuit carefully to minimize parasitic effects and maintain the lowpass filter’s intended frequency response.
A carefully designed lowpass filter provides a stable frequency response, allowing radar systems to accurately differentiate between signal and noise, even in high-EMI environments typical in military operations.
Best Practice 5: Test and Validate Your Lowpass Filter Design
Testing and validating your lowpass filter design verifies how it performs under the intended operating environment. Real-world conditions often introduce unforeseen challenges, requiring your filter to maintain its expected frequency response despite external influences.
Consider the following best practices to achieve optimal lowpass performance despite fluctuating parameters:
- Replicate Operating Environment. Include temperature variations, interference sources, and load conditions to reflect expected scenarios accurately.
- Use Precise Test Equipment. Measure performance parameters such as cut-off frequency, insertion loss, and signal attenuation.
- Identify and Address Issues Early. Examine the lowpass filter under various conditions to determine potential problems and adjust the design accordingly.
Achieve Lowpass Filter Design Excellence with Q Microwave’s Seasoned RF Experts
Different use cases require customized approaches to lowpass filter design, but one constant remains: precision is essential to achieve optimal signal performance.
"Speed, power, and size are key drivers of filter innovation, but they often work against each other. Q Microwave creates custom lowpass filters that achieve the ideal balance between these factors, delivering top performance against various parameters.”
- David Higginson, MBA, PMP, Director of Business Development, Q Microwave
Partner with Q Microwave for off-the-shelf and custom lowpass filter solutions expertly engineered to fulfill your project’s technical requirements. Our certified team of experts brings over 25 years of experience with advanced projects across aerospace and defense industries. We adhere to stringent standards, such as AS 9100 and ISO 9001, to provide reliable, precision-engineered products.
Contact Q Microwave today to deliver a comprehensive RF solution that meets your project's requirements.